Los automóviles modernos poco tienen que ver con aquellos que se fabricaban a principios del siglo XX, y de la misma manera ha cambiado el mercado: si antes un mismo modelo podía fabricarse durante décadas sin apenas cambios, en la actualidad rigen la innovación y las modas. Y, en este marco de continua transformación, la colaboración entre socios tecnológicos cobra una gran importancia, como en el caso de Matrici, Quantech ATZ, la Sociedad Fraunhofer y el CESGA, unidos en un mismo proyecto dentro del programa europeo Fortissimo.
Matrici es una empresa integrada en la División de Conformado y Ensamble, dentro del Área Industrial de la cooperativa vasca Grupo Mondragón, y se dedica principalmente a la fabricación por estampación en metal de piezas exteriores de carrocería y refuerzos para el sector automovilístico, en tanto que Quantech ATZ es responsable del desarrollo y adaptación del software Stampack, específico para el cálculo por el método de elementos finitos de ese tipo de piezas. Por su parte, el Fraunhofer Institute for Algorithms and Scientific Computing SCAI, de Alemania, actuó como servidor de licencias de software, mientras que el CESGA o Centro de Supercomputación de Galicia aportó la capacidad de ejecutar HPC, esto es, High Performance Computing o Computación de Alto Rendimiento, gracias a sus superordenadores y redes de computación distribuída.
Actualmente, Matrici está desarrollando los procesos necesarios para trabajar con aluminio y con aceros convencionales de alta resistencia (HSS), que permiten una producción a menor coste de vehículos más ligeros, ayudando a los fabricantes a adaptarse a las exigentes normativas de emisiones y al desarrollo del coche eléctrico. También en los últimos años, en el sector del automóvil se están produciendo importantes cambios en términos de requisitos para los nuevos modelos, con más pruebas de choque de seguridad, pero con menos peso, para lograr una reducción de consumo, y por lo tanto menos contaminación. Es por eso que, para cumplir con estas exigencias, se están incorporando nuevos materiales, porque sus buenas cualidades pueden ayudar a reducir los espesores en distintas partes del chasis, como los pilares o los refuerzos laterales.
La alta resistencia característica de los aceros HSS hace factible el desarrollo de diseños eficientes en términos de masa, lo que ahorra consumo de combustible, al mismo tiempo que genera mayor resistencia a impactos en colisiones. A diferencia de muchos otros materiales, este acero puede alcanzar esas metas sin causar un aumento en el costo total para el fabricante, pero la alta resistencia de este material implica el uso de una mayor presión durante el proceso de estampación y, en general, esto aumenta la dificultad de todo el proceso. Entre los principales problemas asociados de la incorporación de aceros HSS o de aluminio están el severo desgaste de las herramientas de conformado e incluso la ruptura prematura después de hacer pocas piezas. Otro problema importante del empleo de los nuevos materiales es la fuerte recuperación elástica después de la conformación (efecto de resorte), generada por el alto límite de elasticidad de estos materiales.
El trabajo de Matrici abarca todo el desarrollo conceptual de las piezas, su diseño, su fabricación e incluso la adaptación de las plantas de ensamblaje donde luego se combinarán con otras para formar un vehículo completo, y, evidentemente, en ese proceso existen importantes requerimientos en cuanto a aspecto, geometría y comportamiento del componente. Ricardo Muguerza, responsable del proyecto en Matrici, indica que “la precisión en el cálculo de elementos finitos está aumentando en los últimos años, incluyendo algoritmos mejorados y nuevas variables basadas en la aparición de nuevos materiales y en el conocimiento exacto del proceso. Aún hoy se están introduciendo nuevos conceptos para el cálculo, que requieren varios días para un proceso completo de varias operaciones. Debido al gran número de ciclos requeridos para obtener una simulación satisfactoria, desde la industria estamos requiriendo soluciones que puedan abordar el tiempo de cálculo en horas en lugar de días. Para lograr estos requisitos, es necesario el uso de una enorme capacidad de CPU, en la primera etapa de la ingeniería”. Por eso, añade, “lo que pretendíamos por la parte cliente era ejecutar los cálculos con un software de mucha precisión en el menor tiempo posible, porque eso implica que el producto terminado sale antes al mercado: el beneficio para nosotros es el ‘time-to-market’, el hacerlo lo más rápidamente posible, con la mayor precisión y calidad, para así anticiparnos al mercado”, algo que resulta imprescindible para prosperar en el complicado panorama de la economía global actual.
Para acelerar todo el proceso, nos explica Ricardo Muguerza que desde su empresa buscaron “una aplicación de cálculo numérico de sólidos, para el conformado profundo de piezas de materiales avanzados de automoción, lo que es la ‘piel’ o revestimiento exterior (puertas, capó, techo, aletas…), en aceros y aluminio, y partes estructurales como refuerzos de automoción en aceros de alto límite elástico HSS”. Esa aplicación era la que proporcionaba Quantech ATZ, un ‘software vendor’ establecido en Barcelona que desarrolla programas para su utilización en el campo del estampado de metal, o, en palabras de Fernando Rastellini, su director técnico, “lo que nosotros ofrecemos a las empresas es hacer una simulación virtual del proceso, sólo importando conocimientos de la geometría del utillaje, definiendo el material (la chapa de acero que estoy utilizando), y alguno más de los parámetros del proceso, como la fuerza de la prensa, para poder obtener una solución por el método de elementos finitos, de una manera rápida y sencilla, y por supuesto, ofreciendo unos resultados lo más aproximados posible al proceso real”.
Pero además, para satisfacer las necesidades de Matrici se necesitaba también la elaboración de un software de paralelización, porque, como recuerda su responsable de proyecto, “en la industria tenemos la limitación del número de CPUs (Central Processing Units o procesadores) que hay en cada estación de trabajo, y el programa de cálculo numérico que desarrolla y comercializa Quantech está basado en sólidos y requiere de mucho tiempo de computación para ser lanzado a un solo procesador”. La solución pasaba por tanto por la colaboración con una institución que pudiese aportar altas capacidades de cálculo, y ahí, señala Ricardo Muguerza, entraría el CESGA: “dentro de la empresa podemos lanzar a ocho procesadores, pero aún así los tiempos de cálculo son muy elevados, y concretamente, en el prototipo en que hemos estado trabajando, el tiempo de cálculo era de veinticuatro horas lanzado sobre una estación de trabajo a ocho procesadores, y con el mismo prototipo que hemos lanzado en el CESGA con una capacidad cercana a 2.000 procesadores, hemos reducido el tiempo de cálculo un 91%, de veinticuatro horas a dos”.
Además, agrega Muguerza, la simulación numérica permite ahorrar tiempo de otra manera: “antes se hacían los prototipos primero, para ver si resistían las pruebas de ensayo físico, y ahora lo hacemos al revés, primero se hace la fase de cálculo de factibilidad de pieza, para comprobar si es posible o no, y luego se realiza la pieza, de modo que nos anticipamos al chequeo final y comprobamos si el producto es factible antes de que sea fabricado físicamente”. En otro sentido, la anticipación también es, de hecho, uno de los objetivos de cualquier proyecto de I+D+i, o sea, Investigación, Desarrollo e Innovación, claves para mantener el liderazgo de las empresas europeas en la economía globalizada de nuestro tiempo, y al respecto manifiesta Ricardo Muguerza que “estamos asombrados muy positivamente de la respuesta técnica y humana del equipo que ha participado en este proyecto europeo”, opinión que comparte Fernando Rastellini, quien declara que “hemos participado en varios proyectos europeos, y seguiríamos colaborando; lo que es el I+D, potenciado por las ayudas europeas es más fácil, porque si no a las empresas les cuesta invertir”.
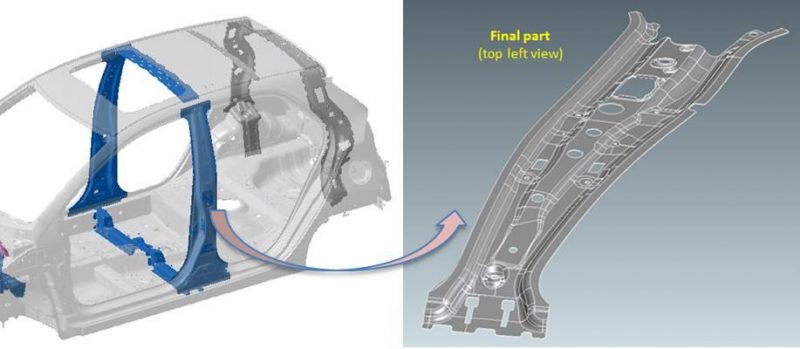
Pilar B de un vehículo, una de las piezas fabricadas en Matrici
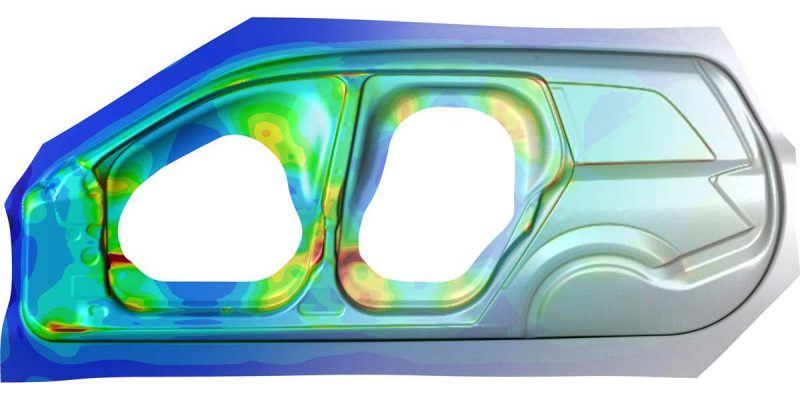
Simulación virtual previa a la fabricación de los prototipos Quantech ATZ